近幾年,在我國的鋼鐵行業,無人工廠、黑燈車間、不見面生產等新形式接連涌現,展現出行業在數字化智能化方面的發展成果,進一步加速了新經濟環境下鋼鐵行業的發展新趨勢。自“供給側改革”以來,我國鋼鐵行業一直走在變革和創新的路上。2019年,中國寶武于智慧制造現場會上正式啟動3000米外的煉鋼3號轉爐“遠程一鍵煉鋼”模式,全流程自動化出鋼程序啟動,“智慧煉鋼”跨出關鍵一步。今年6月,媒體公布的數據顯示,寶武一季度有3家企業的“操作崗位一律機器人”指數達到了50%以上。民企中,河北德龍鋼鐵運用APS系統,進行原材料配比與成本測算,將港口的礦石各項指標、價格以及高爐生產的各種工藝參數錄入系統,通過數據建模的方式進行大數據運算,找出成本最優、質量最優的配料方案以指導采購決策和生產配料。在西南區域,鋼鐵產業同樣已落地各類智慧化項目。在智能制造的生產車間內、在人工減少的產業園區中、在一條條全自動的生產線上,創新的功能、提升的效率、優化的質量不斷呈現,新技術帶來的數字化智能化正在各個企業、各個環節爆發出鮮活的生命力。在積微物聯旗下的達海產業園區內,記者看到不同于以往的傳統物流園,智能化運作流程連貫高效,充滿未來感。車主入園時,智能門崗替代傳統門衛,一瞬間完成車牌識別,同時系統提供園區地圖與導航功能,方便司機快速到達卸貨區域。通過配備的PDA掃描貨品上的標識碼完成每件大宗貨物入庫,通過PDA掃碼還可以追蹤商品所在倉庫的位置和其它精準信息。此刻,存放于倉庫中的大宗貨物的錄入信息已自動上傳于數碼倉系統中,利用園區安裝的500多個360度高清攝像頭,不論是貨主、車主還是園區工作人員都可以借助系統遠程查看貨物的實時情況,或利用VR設備實現“身臨其境”。客戶若要提貨出廠,數碼倉系統會通過與貨主指令協同,配合智能門崗,司機進入業務中心,在自助服務機上,掃描身份證便可辦理出庫手續,到達裝車位完成驗證裝車,確保物資安全。據在場工作人員介紹,達海所提供倉儲服務的安全性是無懈可擊的。“倉庫安裝了無線定位設備,貨物移動全程系統記錄,同時配合運用3D數據孿生技術,對各類非法移動或吊裝進行實時報警,全程監督貨物的移動是否合規有效,確保各類貨物堆放有序、安全可靠。”
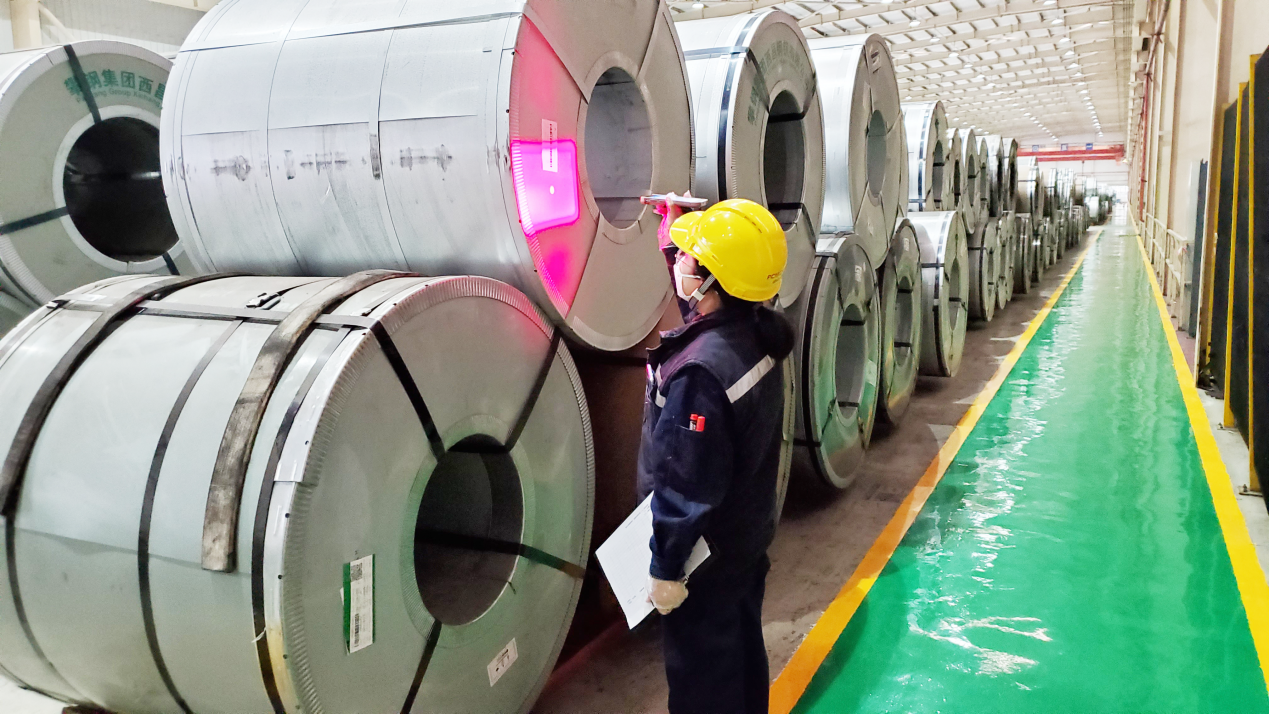
在達海產業園,通過配備的PDA掃描貨品上的標識碼完成每件大宗貨物入庫園區智慧化以后,貨物入庫、出庫變得智能、簡單,貨物安全得以保障。且在疫情期間,優化升級的數碼倉系統進一步推出遠程功能——客戶可在線下提貨單、下加工單、查入出庫、跟進度,打開微信公眾號選擇“園區協同”便能快速了解達海物資庫存、入庫、出庫以及賬單情況。線上線下齊發力,推動達海產業園實現“云倉”“云加工”的布局,進入“數字化”倉儲時代。近日,國家工信部公布了“2019年工業互聯網APP優秀解決方案”名單,積微物聯與阿里云、攀鋼西昌鋼釩共同研發的“攀鋼集團西昌鋼釩ET鋼鐵大腦APP應用解決方案”(以下簡稱“鋼鐵大腦”)成功上榜。鋼鐵大腦運用在攀鋼集團西昌鋼釩有限公司的生產車間內——各個生產工藝充分運用數據進行協同和有序運轉。現場工作人員告訴記者,不像早年間生產鋼鐵需要依賴“老師傅”的個人經驗,而今生產中的每個環節都會有數據作為參照,通過對數據的分析與挖掘,結合人工智能模型,每一道工序都能找到最優的方案,降低加工環節的成本投入。另一邊,在積微物聯公司的生態大屏上,遠在攀枝花的生產車間中,不同高爐和其它不同生產環節的各項數據實時變動都顯示在屏幕上。公司技術人員可以遠程查看生產情況,分析數據,再將數據分析反饋至車間,優化工藝、服務生產。而這個“神奇”的過程被專業人士稱為“為傳統鋼鐵企業裝上工業大腦”。積微物聯技術負責人為記者介紹道,“我們生產線上安裝了上萬個傳感器。以往采集的數據沒有真正用起來,現在我們與阿里聯手打造的工業大腦可以讓數據‘開口說話’,幫助傳統鋼鐵生產提質降本。一套鋼鐵大腦的引入可以幫企業節約上千萬元的成本。”作為生產車間的重要組成部分,生產線的智能化水平是衡量車間智慧化程度的重要指標。在攀鋼集團攀枝花釩廠,由成都星云智聯科技有限公司(以下簡稱“星云智聯”)主導打造的“釩氮合金智能產線”正在以一種無人少人化、數字化、智能化的方式高速運轉——無人吊車、AGV叉車如同機器人在車間“行走”,生產物料自動運轉,機械臂卸料裝置取代人工卸料,生產工藝過程僅需2名職工在可視化遠程集控中心進行操作,便可實現生產自動化、產線智能化、過程可視化、管理智慧化。生產完成后,自動化的包裝線又進一步實現了對釩氮合金產品的自動破碎、輸送、粗稱和封口等步驟。整個“釩氮合金智能生產線”融合了信息、制造、控制、通信、人工智能和5G、工業網關、數字仿真、邊緣計算等先進技術,率先在國內釩制造領域實現了智慧物聯傳輸、生產物料自主轉運、產品自動包裝、全線遠程可視集控和物流連續自動等。
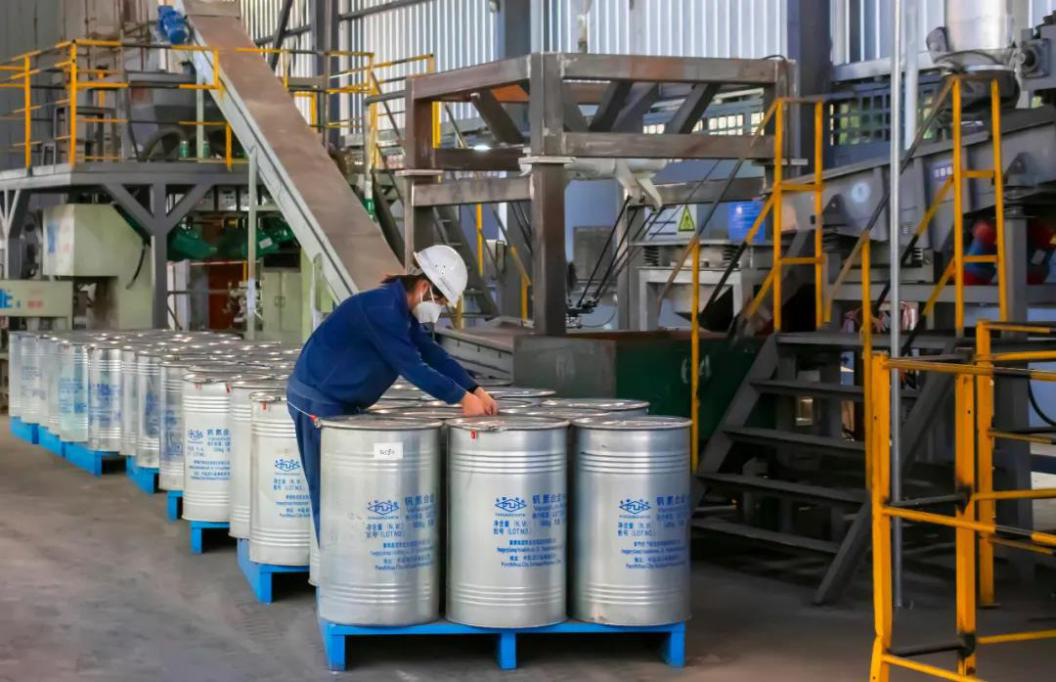
星云智聯主導打造的釩氮合金智能產線為生產效率的提升貢獻力量
因釩氮合金生產工藝復雜,生產條件要求高,在2018年星云智聯投入產線建設以前,國內還沒有任何一家釩氮合金生產企業進行全流程自動化、智能化生產方面的嘗試。星云智聯的探索,率先在業界示范性地實現了“兩化融合、智能制造”,讓傳統制造行業看到了數字化智能化轉型升級的未來前景,同時取得提質增效、低耗高產、安全高效、綠色環保、智慧管理等方面的顯著成效。“以前我們生產釩氮合金,靠人工進行上卸料、配料、物料倒運和包裝等操作,勞動強度大,且易產生產品成分波動和揚塵等問題,現場環境衛生難以保持。現在,我們的職工在可視化遠程集控中心就能清晰地掌握現場生產過程的重要控制參數變化和物料轉運情況,及時發現設備故障,生產作業效率得到了明顯提升,現場作業環境也得到了極大改善。”釩氮合金作業區負責人如是說。瞄準“智能制造”和改變傳統生產方式的目標,星云智聯集中力量持續投入到數字化智能化產線的打造中——除“釩氮合金智能產線”外,星云智聯還與北京工業大數據中心合作開展了“萬能二線產線數字化建設”項目——幫助企業優化檢修周期,提高調整效率,增進設備自診斷。更為重要的是,通過鋼軌過程數據“米跟蹤”技術,確保了每一米鋼軌的生產過程狀況可追蹤溯源,實現了國內首條鋼軌生產線的數字化和生產過程的可視化管控,進一步提升了成材率和鋼軌質量,樹立了型材數字化產線的樣板。不僅如此,星云智聯還在“礦業公司選鈦廠兩化融合示范線”建設項目中,通過選鈦MES及配套建設,補齊了選鈦廠自動化控制和生產管理信息化的短板,實現了生產的集中控制——操作室數量大幅減少,效率的提升、能耗的降低以及工作崗位的優化,無一不為選鈦產品的質量穩定性和高水平的生產管理能力貢獻了科技賦能的無窮魅力。作為深耕于高端汽車板剪切加工的攀中伊紅公司,于2019年7月通過了重慶市經信委的評選認定,成功入選“重慶市智能工廠”,開啟了數字化智能工廠建設的新篇章。在攀中伊紅公司代表其智慧化發展的三個數字化車間內,自動化加工正“按著節奏”頗有秩序地進行著。車間通過引進飛剪整理機組、二期激光拼焊機、異形焊接原料智能精剪、拆堆垛機器人等自動化設備及軟件,助力數字化智能化轉型,生產變得更高效,質量也更加可靠。通過智能工廠建設,攀中伊紅整體生產運營成本降低16%, 生產效率提高20%,能源利用率提高20%,其自動化、智能化應用已達到國內先進水平。相關負責人表示,“不論在產品研發還是生產制造上,我們堅持充分借助信息技術和智能手段,提升智能制造水平及服務能力,并最終落腳到提升產品品質上”。堅持產品品質,更好地服務客戶,是攀中伊紅獲得長安、五菱、長城、吉利等知名汽車主機廠持續信賴的不二秘鑰。地處西南區域,積微物聯、星云智聯,攀中伊紅,還有無數不同規模的傳統鋼鐵企業,在新一輪工業革命的背景下,在“新經濟”“新基建”“成渝雙城經濟圈”“新時代西部大開發”等一系列政策的引導下,正積極搶抓機遇,集體性地將新技術手段引入到生產環節,帶來“工業互聯網”“智能制造”“智慧工廠”“智能生產線”等新概念、新實踐、新成果的頻頻出現,并匯聚迸發出新的信號——以堅持創新的信念和行動,不斷革新傳統制造、傳統生產方式、傳統管理模式,推動智能制造向前發展,推動傳統行業數字化智能化轉型升級,共同展望“產業變革、智造強國”的智慧未來。
返回列表